Discover how robot manipulators are transforming the welding industry, enhancing efficiency, quality, and safety. Explore the precision, productivity, and skill enhancement opportunities they offer, and envision the future of robotic welding technology.
Discover how robot manipulators are transforming the welding industry, enhancing efficiency, quality, and safety. Explore the precision, productivity, and skill enhancement opportunities they offer, and envision the future of robotic welding technology.
Outline:
1. Introduction
A. Definition of robotic welding
B. Importance of robot manipulators in the welding process
2. The Efficiency of Robot Manipulators
A. Precision and repeatability
B. Increased productivity and output
C. Reduction of human error and fatigue
3. Enhanced Weld Quality
A. Consistency in weld bead formation
B. Control over welding parameters
C. Minimization of defects and rework
4. Safety Considerations
A. Reduced exposure to hazardous environments
B. Minimized risks of injuries and accidents
C. Compliance with safety regulations and standards
5. Skill Enhancement for Welding Technicians
A. Transitioning to robot programming and operation
B. Upskilling in troubleshooting and maintenance
C. Adaptation to evolving technological advancements
6. Challenges and Future Outlook
A. Initial investment costs and ROI considerations
B. Integration with existing welding processes
C. Anticipated developments in robot manipulator technology
7. Conclusion
A. Recap of the pivotal role of robot manipulators in robotic welding
B. Affirmation of their contribution to efficiency, quality, and safety
C. Encouragement for welders to embrace and harness the potential of automation
8. Summary
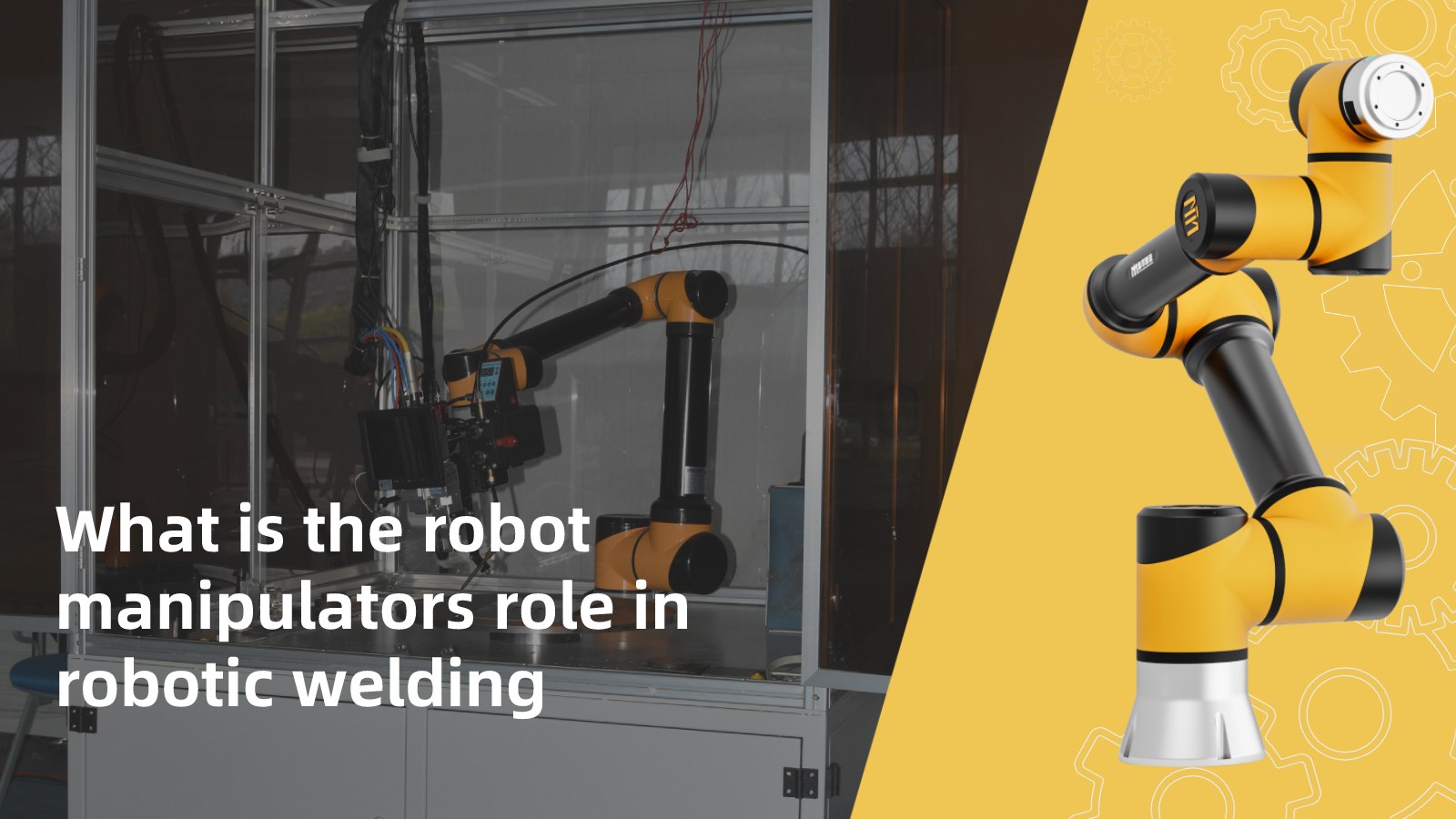
1. Introduction
A. Definition of robotic welding
Robotic welding involves the use of automated systems, including robot manipulators, to perform welding tasks. These systems are programmed to execute precise movements and control welding parameters, offering numerous advantages over traditional manual welding methods.
B. Importance
Robot manipulators play a crucial role in robotic welding by providing the mechanical means to position and move the welding tool with high accuracy and repeatability. They serve as the arms of the welding robot, executing welds according to predefined instructions, thereby streamlining the welding process and enhancing overall efficiency.
2. The Efficiency of Robot Manipulators
01
A. Precision and repeatability
Precision and repeatability are fundamental aspects of robot manipulators, allowing them to consistently execute welds with minimal deviation from the desired path. This precision ensures uniformity in weld quality across multiple workpieces, leading to increased productivity and reduced scrap rates.
02
B. Increased productivity and output
By automating repetitive welding tasks, robot manipulators contribute to higher throughput and output in welding operations. Their ability to work continuously without fatigue or breaks further enhances productivity, making them indispensable assets in high-volume manufacturing environments.
03
C. Reduction of human error and fatigue
Human error is a common concern in manual welding, but robot manipulators help mitigate this risk by following precise instructions without deviation. This reduction in human error not only improves the overall quality of welds but also minimizes the need for rework, saving both time and resources.
3. Enhanced Weld Quality
01
A. Consistency in weld bead formation
Consistency in weld bead formation is a hallmark of robot manipulators, as they can precisely control parameters such as travel speed, arc length, and wire feed rate. This consistency results in uniform weld profiles and penetration depths, regardless of variations in operator technique or environmental conditions.
02
B. Control over welding parameters
The ability to control welding parameters with precision enables robot manipulators to produce welds of superior quality compared to manual methods. By maintaining optimal conditions throughout the welding process, they minimize defects such as porosity, lack of fusion, and excessive spatter, leading to higher-quality finished products.
03
C. Minimization of defects and rework
Minimizing defects and rework not only improves the aesthetic appearance of welded components but also enhances their structural integrity and performance. This reduction in defects translates to cost savings for manufacturers by reducing scrap rates and minimizing the need for post-welding inspection and rework.
Safety Considerations
01
A. Reduced exposure to hazardous environments
Robot manipulators contribute to workplace safety by reducing the need for human operators to be in close proximity to the welding process. This minimizes the risk of exposure to hazards such as fumes, sparks, and arc radiation, thereby protecting workers from potential health and safety risks associated with welding operations.
02
B. Minimized risks of injuries and accidents
By automating repetitive and physically demanding tasks, robot manipulators help mitigate the risk of injuries and ergonomic issues among welding personnel. This includes reducing the risk of musculoskeletal disorders associated with manual welding, such as strains, sprains, and repetitive motion injuries.
03
C. Compliance with safety regulations and standards
Compliance with safety regulations and standards is essential in welding operations, and robot manipulators play a crucial role in ensuring adherence to these requirements. By following predefined safety protocols and operating within established parameters, they help maintain a safe working environment and minimize the likelihood of accidents or regulatory violations.
4. Skill Enhancement for Welding Technicians
A. Transitioning to robot programming and operation
Transitioning to robot programming and operation opens up new opportunities for welding technicians to expand their skill sets and advance their careers. By acquiring proficiency in robotic welding technologies, technicians can enhance their value to employers and position themselves for roles that require expertise in automation and robotics.
-
Upskilling in troubleshooting and maintenance
Upskilling in troubleshooting and maintenance is essential for welding technicians working with robot manipulators, as they are responsible for ensuring the continued operation and performance of these systems. This includes diagnosing and resolving technical issues, performing routine maintenance tasks, and optimizing robot programming for efficiency and quality.
-
Adaptation to evolving technological advancements
Adaptation to evolving technological advancements is a continuous process for welding technicians, as new developments in robot manipulator technology continue to emerge. Staying abreast of these advancements through ongoing training and professional development enables technicians to remain competitive in the field and capitalize on the latest innovations in robotic welding.
VI. Challenges and Future Outlook
A. Initial investment costs and ROI considerations
Initial investment costs and ROI considerations are key factors that may influence the adoption of robot manipulators in welding operations. While the upfront costs of implementing robotic welding systems can be significant, manufacturers must weigh these expenses against the long-term benefits in terms of increased productivity, improved quality, and reduced operational costs.
B. Integration with existing welding processes
Integration with existing welding processes presents challenges in terms of compatibility, workflow optimization, and coordination with other production equipment. Manufacturers must carefully plan and execute the integration of robot manipulators into their existing operations to minimize disruptions and maximize the efficiency gains associated with automation.
C. Anticipated developments in robot manipulator technology
Anticipated developments in robot manipulator technology hold promise for further enhancing the capabilities and performance of robotic welding systems. This includes advancements in areas such as artificial intelligence, sensor technology, and collaborative robotics, which have the potential to revolutionize the way welding tasks are performed and managed in the future.
VII. Conclusion
A. Recap of the pivotal role of robot manipulators in robotic welding
Robot manipulators play a pivotal role in robotic welding, offering a multitude of benefits in terms of efficiency, quality, and safety. Their precision, repeatability, and ability to control welding parameters enable manufacturers to achieve higher levels of productivity and produce welds of superior quality compared to manual methods.
B. Affirmation of their contribution to efficiency, quality, and safety
By reducing human error, minimizing defects, and enhancing workplace safety, robot manipulators contribute to the overall competitiveness and sustainability of welding operations. Embracing automation and harnessing the potential of robot manipulators enables welding technicians to adapt to changing industry trends and position themselves for success in the evolving landscape of manufacturing.
C. Encouragement for welders to embrace and harness the potential of automation
Moving forward, the continued advancement of robot manipulator technology promises to further enhance the capabilities and performance of robotic welding systems, driving innovation and efficiency in the welding industry. By staying informed, proactive, and adaptable, welding professionals can seize the opportunities presented by automation and pave the way for a brighter future in welding and fabrication.
Summary:
In the realm of welding, the integration of robot manipulators has revolutionized the landscape, offering a myriad of benefits from enhanced efficiency to improved safety. The precision and repeatability of robot manipulators contribute significantly to increased productivity and output, while simultaneously reducing human error and fatigue. Moreover, these manipulators ensure a higher weld quality by maintaining consistency in bead formation and providing control over welding parameters, thereby minimizing defects and rework.
From a safety standpoint, robot manipulators mitigate risks by reducing exposure to hazardous environments and minimizing the likelihood of injuries or accidents, aligning with stringent safety regulations. Furthermore, they present an opportunity for welding technicians to enhance their skills by transitioning to robot programming and operation, thus positioning themselves at the forefront of technological advancements.
Despite the initial investment costs and integration challenges, the future outlook for robot manipulators in robotic welding remains promising, with anticipated developments paving the way for even greater efficiencies and capabilities. Ultimately, the role of robot manipulators in welding is indispensable, offering a pathway toward increased efficiency, quality, and safety in the welding industry.