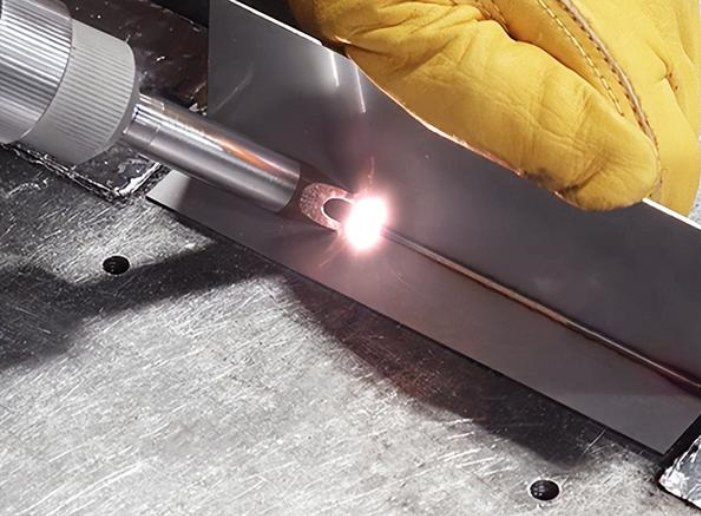
In the dynamic landscape of industrial manufacturing, welding stands as a cornerstone process, essential for fabricating everything from automotive components to aerospace structures. As demands for precision, efficiency, and safety continue to escalate, the integration of robots into welding operations has emerged as a transformative solution. This article delves into the myriad reasons why robots have become indispensable in the realm of industrial welding.